Alternative aux résines époxy, polyesters ou polyuréthane, le p-DCPD est un matériau léger aux qualités exceptionnelles, qui satisfait aux exigences les plus extrêmes. Il avait néanmoins l’inconvénient de dégager une forte odeur caractéristique, incompatible avec un usage en intérieur. Pour répondre aux besoins de l’industrie automobile, l’entreprise DEMETA et son client H+S (Allemagne) ont mis au point un procédé de production de pièces p-DCPD sans odeur. Pour en savoir plus, nous avons interviewé Ralph HEDEL, directeur commercial de DEMETA.
DEMETA est une société française de chimie verte créée en 2011. Cette spin-off de l’université de chimie de Rennes utilise son savoir-faire en catalyse pour la synthèse de produits de chimie fine et de polymères techniques comme le NexTene™.
Techniques de l’ingénieur : NexTene™ est présentée comme une résine haute-performance. Pouvez-vous nous en dire plus à son sujet ?
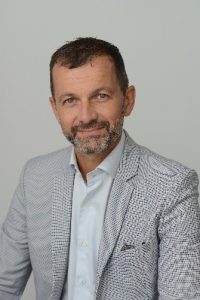
Ralph HEDEL : La résine NexTene™ que nous commercialisons est une nouvelle famille de polymères. Elle est composée de poly-DCPD, un matériau qui combine les avantages des thermoplastiques, des thermodurcissables et des fluoropolymères.
Son développement a pu être accéléré grâce au programme EIC Accelerator 2020 (du Fonds du Conseil européen de l’innovation) qui nous a permis de bénéficier d’un financement mixte de 4,8 millions d’euros. Nous sommes d’autant plus ravis d’avoir été choisis que ce programme est très sélectif : seulement 75 projets ont été retenus sur les 1 850 entreprises européennes postulantes.
Nous travaillons actuellement avec H+S Automotive pour développer des cadres de toit ouvrant pour voiture. Pour cette entreprise allemande du secteur automobile qui possède une expérience des procédés de mise en œuvre du p-DCPD, ce matériau était ainsi un choix logique.
Pourquoi le p-DCPD est-il un matériau intéressant pour les applications automobiles ?
Le p-DCPD possède une résistance élevée et supporte des sollicitations importantes, mais il a également l’avantage d’être extrêmement léger, avec une densité de 1,03, soit 15 % à 20 % plus léger que les matériaux conventionnels tels que époxy, polyesters ou polyuréthane. Compte tenu du malus au poids qui touche les véhicules lourds et du malus CO2, les constructeurs cherchent désormais à alléger les véhicules.
Ainsi, un cadre de toit ouvrant fabriqué avec NexTene™ ne pèse plus que 900 g, contre 1,8 kg auparavant pour un cadre d’acier, ce qui a un impact positif sur la consommation de carburant. Par ailleurs, ce gain de poids est d’autant plus important que la pièce est située sur le toit du véhicule, ce qui permet d’améliorer la stabilité dans les courbes à haute vitesse et d’améliorer le confort des passagers.
Quel était le point de départ de cette collaboration avec H+S Automotive ?
Si le p-DCPD est un matériau fantastique du point de vue de ses performances mécaniques et thermiques, il a l’inconvénient de dégager une odeur très particulière.
Cette odeur, bien qu’elle ne soit pas le signe d’une dangerosité quelconque, demeure perceptible par le cerveau humain à des niveaux de concentration très faible. C’est donc à cause de cette caractéristique que ce matériau a jusqu’ici été banni des intérieurs de véhicules.
Après avoir découvert les nombreux avantages du p-DCPD, l’un des clients de H+S Automotive nous a ainsi sollicités afin de mettre au point un système permettant de produire des pièces en p-DCPD sans odeur.
Avez-vous réussi à surmonter ce problème d’odeur ?
Au cours de ce projet, de nombreux essais ont été réalisés et caractérisés. Les différentes formulations ont été testées par un laboratoire accrédité, qui a suivi des protocoles de tests très stricts.
Le protocole VDA 270, permettant la détection des caractéristiques olfactives, consistait à faire sentir le produit par un panel de nez humains chargés de fournir une évaluation sur le niveau d’odeur. Après deux ans de travaux et de multiples échantillonnages, nous avons ainsi trouvé la formulation permettant de réduire les odeurs à un niveau acceptable.
Suite à ces essais concluants, nous sommes donc passés à l’étape suivante, c’est-à-dire la fabrication de pièces à échelle industrielle réelle. Ces pièces ont ensuite été soumises à nouveau au protocole VDA 270, ce qui a amorcé la commande de préséries.
Nous sommes actuellement à la quatrième étape de validation. Celle-ci consiste à tester le produit sur 200 véhicules qui ont commencé leurs essais de mise à la route pour 6 mois.
Travaillez-vous sur d’autres applications du p-DCPD ?
À la suite de ces travaux, nous allons maintenant proposer ce produit à certains de nos clients traditionnels. Le p-DCPD s’adresse principalement à des petites et moyennes séries de pièces de carrosserie. Ce nouveau grade sera un matériau très utile pour fabriquer des intérieurs de cabine et des pavillons de toit à destination de machines agricoles, de camions ou d’engins de chantier, de façon très économique.
Réagissez à cet article
Vous avez déjà un compte ? Connectez-vous et retrouvez plus tard tous vos commentaires dans votre espace personnel.
Inscrivez-vous !
Vous n'avez pas encore de compte ?
CRÉER UN COMPTE