La start-up française présente à la fois en Europe et en Asie réalise un inventaire du catalogue de ses clients et leur propose des solutions de réplication optimisées à plusieurs niveaux. Afin d'assurer cet ambitieux service, la jeune pousse compte sur un réseau de sous-traitants présents partout dans le monde. C'est ce qu'explique Paul Guillaumot, fondateur et CEO de Spare Parts 3D.
Lorsqu’il a créé Spare Parts 3D en 2016, l’objectif de Paul Guillaumot était de pouvoir fournir aux entreprises une solution de réplication de leurs pièces détachées. Grâce à la création d’un software, l’entreprise est capable de réaliser un inventaire numérique des pièces de leurs clients. Le fondateur et CEO de cette start-up affirme que cette solution a de multiples avantages.
Techniques de l’Ingénieur : Comment avez-vous eu l’idée de créer Spare Parts 3D ?
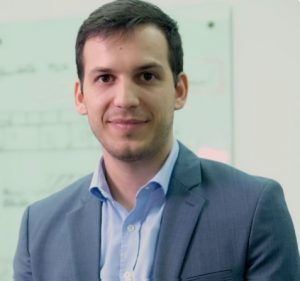
Paul Guillaumot : Je me suis rendu compte du potentiel des technologies de fabrication additive. Mais surtout, j’ai eu une visibilité à la fois du niveau de maturité industrielle et du potentiel. Je me suis donc mis en quête d’une solution qui me permettrait de fournir un système d’inventaire numérique et de production à la demande de pièces détachées. Cela a été motivé par une envie de réduire les stocks, les délais d’approvisionnement et les problèmes d’obsolescence. En clair, mon but était de régler le problème de la pièce détachée. Or, ce n’est pas simple.
Quel est ce problème ?
Dans les entreprises, il n’y a jamais la bonne pièce au bon endroit au bon moment. Et malgré les stocks parfois faramineux de pièces détachées présents chez les industriels, les niveaux de services ne sont pas toujours optimaux.
Qui sont vos clients ?
Ce sont des grands industriels. Par exemple, nous comptons parmi nos clients des géants de l’électroménager. Nous travaillons avec eux depuis quelques années déjà. Pour eux, nous fabriquons des petites ou moyennes pièces à la demande. Ensuite, nous travaillons avec d’autres industriels qui exercent dans l’industrie lourde. Ils sont par exemple dans la pétrochimie ou l’aciérie. Nous pouvons aussi travailler avec des sociétés qui exercent dans des secteurs très réglementés. Mais nous ne sommes pas forcément en développement commercial sur ces secteurs-là, parce que les délais sont trop longs. Cela est lié aux certifications, aux approbations systématiques nécessaires pour ces secteurs, qui de fait bougent très lentement.
Pourquoi vous êtes-vous lancé dans le marché de la fabrication additive ?
Aujourd’hui, la fabrication additive représente environ 11 milliards d’euros de chiffre d’affaires annuel. Et selon les estimations du cabinet de conseil en stratégie américain McKinsey, ce chiffre pourrait même atteindre quelques centaines de milliards d’ici 2025. Mais personnellement, je placerais plutôt cette barre à 2030. Aujourd’hui, 14 % des industriels dans le monde ont fait imprimer des pièces détachées. D’ici les deux prochaines années, ils seront 46 %. Nous avons réussi à identifier pourquoi ils ne sont que 14 %. La grosse difficulté pour pouvoir faire des grandes quantités de pièces, c’est d’abord d’identifier les pièces qui sont productibles et de trouver quelles sont les technologies qui peuvent être utilisées. Parce que l’impression 3D, ce n’est pas qu’une seule technologie, mais plutôt plusieurs qui peuvent intégrer également plein de matières. À l’heure actuelle, nous avons 2 500 solutions techniques dans notre software.
Comment fonctionne votre solution ?
Nous digitalisons la chaîne d’approvisionnement de pièces détachées. Concrètement, nous nous rendons chez l’industriel et nous analysons les données issues des systèmes d’information sur des ensembles de plusieurs dizaines de milliers de pièces. Ensuite, nous leur présentons ce qui peut être imprimé et les technologies pour le faire. Au lieu d’avoir un circuit de production conventionnel avec des grosses usines, beaucoup de transport et de stockage, on crée des inventaires de pièces digitaux. Puis on fait de la production à la demande locale, à l’aide de machines d’impression 3D. Notons que nous n’effectuons pas ces tâches en interne. Nous gérons un réseau de production d’entreprises spécialisées dans la fabrication additive. Ce sont les services bureaux. Ces entreprises sont des spécialistes qui font beaucoup de prototypage. Elles travaillent localement avec les industriels de leur région. Nous leur achetons la capacité machine sur différentes matières, machines, technologies dont on a besoin et là où on en a besoin. C’est-à-dire dans plus de 25 pays dans le monde.
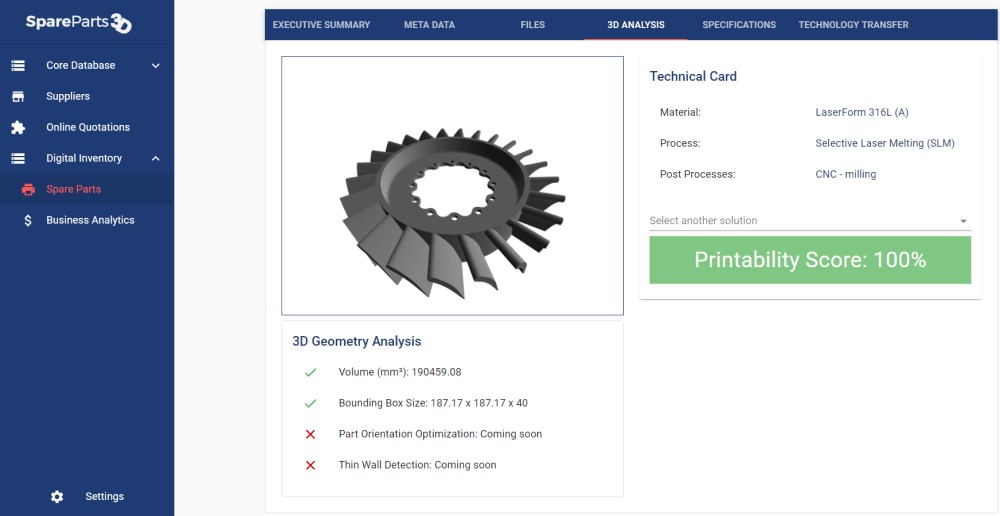
Quels sont les avantages pour vos clients ?
Notre point fort est notre solution de software 3 en 1. À l’aide de cela, nous pouvons créer des inventaires digitaux beaucoup plus rapidement et efficacement. Et à moindre coût. De plus, cela permet d’avoir des inventaires prêts à l’impression 3D. Ainsi, nous regroupons toutes les infos nécessaires pour sourcer les pièces. Et derrière, nous allons jusqu’à connecter avec nos sous-traitants pour pouvoir demander et gérer en temps réel la production.
Comment parvenez-vous à créer des pièces d’une manière plus optimisée que vos clients ?
Nous réalisons une analyse d’imprimabilité des pièces. Par exemple, sur un catalogue de 20 000, nous sommes capables de dire lesquelles sont plus ou moins imprimables. Le client nous donne un inventaire numérique de ses pièces, et nous l’analysons pour vérifier s’il est possible ou non de les réimprimer. Notre avantage est d’avoir une démarche systématique, automatisée, qui peut être déployée sur un très grand nombre de pièces.
Sur quels critères se définit l’imprimabilité d’une pièce ?
Dans un premier temps, il faut savoir si la pièce peut entrer dans la machine. C’est important parce que chaque technologie a des limites sur la taille des pièces qu’elle peut produire. Il y a aussi des contraintes liées aux formes géométriques. Après, il faut vérifier ce qui a trait à l’analyse fonctionnelle, c’est-à-dire tous les besoins techniques de la pièce. Par exemple, les contraintes mécaniques attendues en termes de flexion ou en traction, l’élongation, la température d’utilisation ou encore l’absorption en eau. L’objectif pour nous est de rechercher une solution technique qui réponde à un maximum de critères. En règle générale, nous parvenons à respecter environ 80 % des critères. Un ingénieur vient ensuite vérifier si ces légères différences n’entravent pas le bon fonctionnement de la pièce.
Les pièces sont-elles imprimées dans le même matériau que la pièce originale ?
Ce n’est pas toujours le cas. Dans de nombreux cas, l’utilisation d’une matière différente n’a pas d’incidence négative sur le fonctionnement de la pièce détachée.
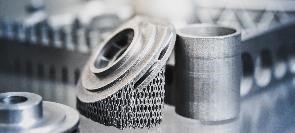
Votre solution présente-t-elle des intérêts écologiques ?
Oui, à trois niveaux. Premièrement, lorsque l’on se trouve face à de l’obsolescence, la pièce détachée évite de remplacer la machine entière. Deuxièmement, nous réduisons le besoin en matière en imprimant directement la pièce à sa bonne forme. Cela permet d’économiser environ 40 % de matière. Enfin, notre solution permet de relocaliser la production. De ce fait, les transports sont drastiquement réduits.
Réagissez à cet article
Vous avez déjà un compte ? Connectez-vous et retrouvez plus tard tous vos commentaires dans votre espace personnel.
Inscrivez-vous !
Vous n'avez pas encore de compte ?
CRÉER UN COMPTE