Depuis des décennies, l’Union européenne fait face à un important déficit en protéines pour nourrir les animaux d’élevage. Pour rétablir notre souveraineté alimentaire et réduire notre dépendance aux ingrédients importés, comme le soja, il est donc urgent de trouver des sources de protéines alternatives. Le projet européen SYLFEED a proposé de transformer les coproduits de l’industrie du bois en protéines pour l’alimentation des poissons. Retour sur une initiative prometteuse.
Charles-Henri Nicolas et Alexandre Garcia, de la société ARBIOM qui est à l’origine de la technologie innovante au cœur du projet SYLFEED, ont accepté de répondre à nos questions.
SYLFEED était un projet européen financé à hauteur de 8,7 M€ (sur un budget total de 10 M€) par le Bio Based Industries Joint Undertaking dans le cadre du programme de recherche et innovation Horizon 2020 de l’Union Européenne sous l’accord de financement n°745591. Ce projet européen intégrait un consortium de 10 partenaires, dont ARBIOM assurait le rôle de coordinateur. Débuté en 2017, il s’est achevé 4 ans plus tard, en août 2021.
Techniques de l’Ingénieur : Pourquoi rechercher des sources d’alimentation animale alternatives ?
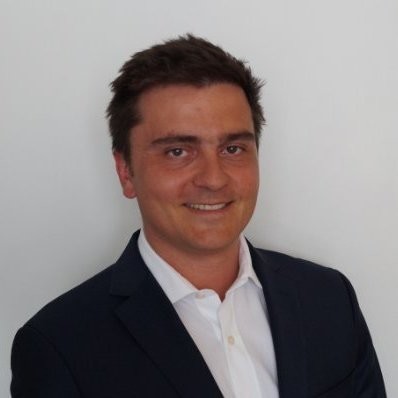
Charles-Henri Nicolas : Cela fait 40 ans que l’Europe est confrontée à un déficit en protéines destinées aux élevages. À l’heure actuelle, 70 % de la nourriture qui est consommée par les élevages européens est ainsi importée. Dans le cas de l’alimentation piscicole, ces sources de nourriture – farines de poisson ou de soja – ont plusieurs inconvénients. D’une part elles ne sont pas durables, d’autre part elles posent des problèmes en termes de besoins stratégiques et ne favorisent ni l’emploi local ni le développement de nos filières.
Quel était le rôle d’ARBIOM dans le projet SYLFEED ?
C-H. N. : L’objectif du projet SYLFEED était de faire passer à l’échelle industrielle le procédé de fermentation de la biomasse lignocellulosique développé par ARBIOM et qui permet la conversion en protéines. Nous avons donc cherché à réunir différents partenaires, dans le but de créer une chaîne de valeur qui soit la plus locale possible. ARBIOM est ainsi à l’origine de ce projet qui a réuni 10 partenaires du nord-ouest de l’Europe.
Pour le sourcing de résidus de bois, nous nous sommes tournés vers Norske Skog, un papetier implanté à Golbey, dans les Vosges. Pour le prétraitement et la fermentation, nous nous sommes appuyés sur les sociétés Prayon et Rise Processum et nous avons utilisé les équipements des plateformes Bioprocess Pilot Facility et Bio Base Europe Pilot Plant pour la mise en production. La formulation et l’analyse des produits ont été confiées aux sociétés Matís et Laxá, ainsi qu’à Skretting, un producteur mondial d’aliments pour poissons.
Par ailleurs, ce projet a également fait l’objet d’une étude ACV, qui a été confiée à Norsus, un autre partenaire norvégien.
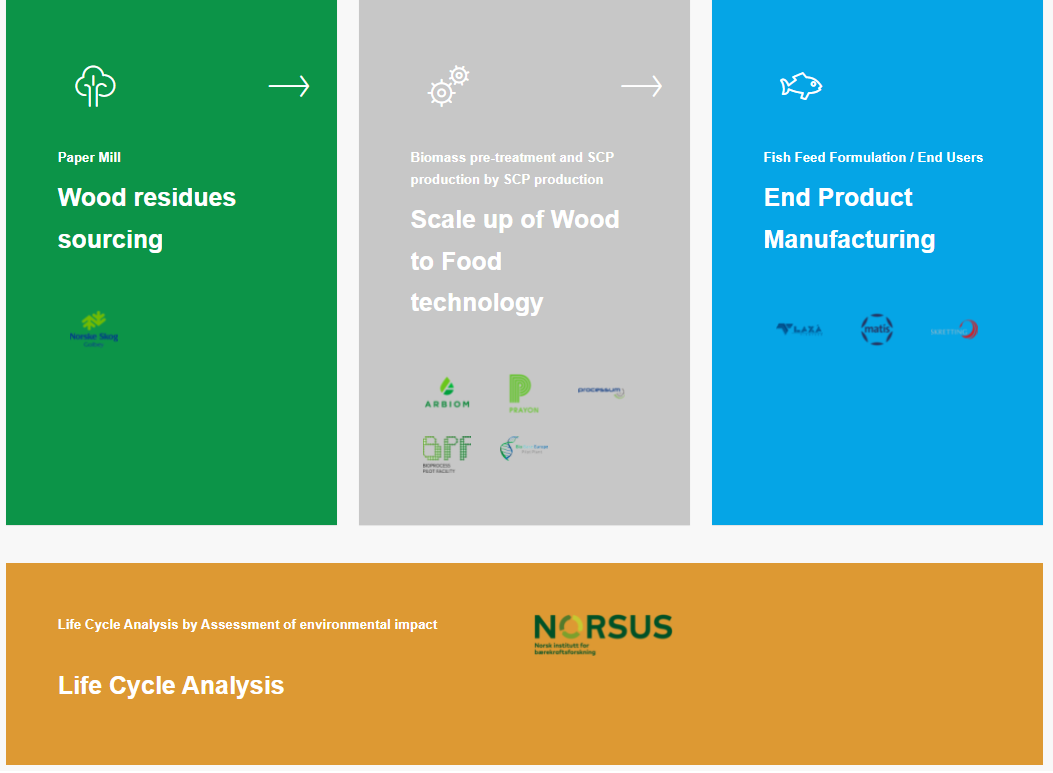
Comment fonctionne le procédé développé par ARBIOM ?
C-H. N. : Notre procédé permet de valoriser la lignocellulose, c’est-à-dire la partie non comestible des végétaux composée de lignine, de cellulose et d’hémicellulose. Il comprend 2 grandes étapes. Dans un premier temps, le bois est fractionné, sa structure est déconstruite afin de revenir aux molécules qui constituent la lignocellulose. Cellulose et hémicellulose sont ensuite hydrolysées et fermentées par des micro-organismes afin de produire des protéines [le produit final a été baptisé SylPro®, NDLR].
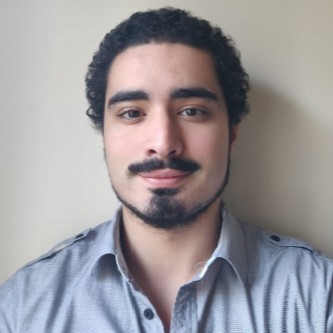
Alexandre Garcia : Par ce processus, nous sommes ainsi capables d’obtenir un ingrédient riche en protéines, en grande quantité, mais aussi de récupérer la lignine. L’ensemble du bois utilisé est donc valorisé.
C-H. N. : Cela fonctionne avec le bois, mais aussi avec toutes sortes de végétaux. Néanmoins, le bois présente un avantage : il peut être approvisionné toute l’année, contrairement aux coproduits agricoles tels que la paille qui sont récoltés une fois par an et nécessitent d’être stockés. Or, le stockage de la paille présente un fort risque d’incendie, un inconvénient qui a été observé dans plusieurs projets de production d’éthanol de 2e génération.
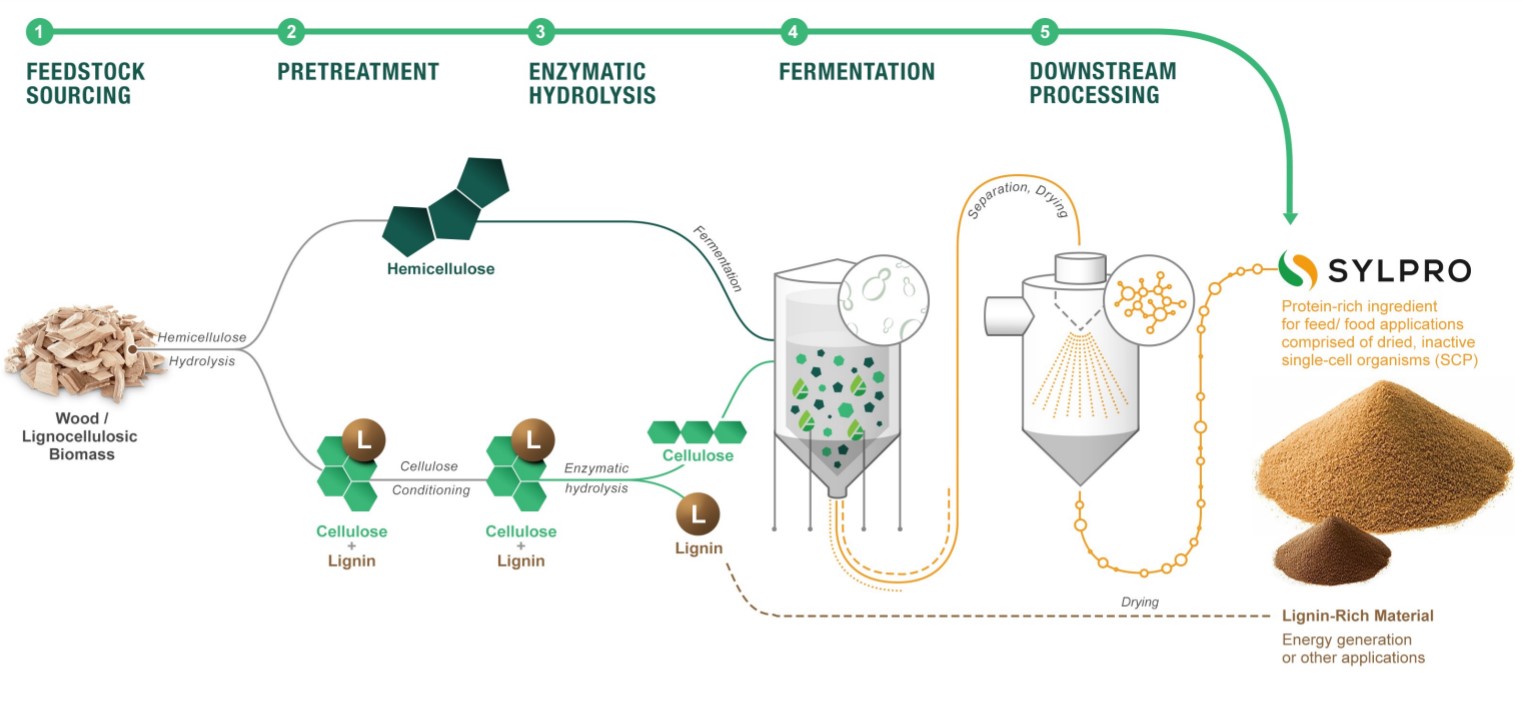
Les résultats étaient-ils à la hauteur de vos attentes ?
C-H. N. : Lorsque nous avons démarré ce projet, notre technologie se situait à un TRL 4 ou 5 [l’échelle TRL, pour technology readiness level, désigne le niveau de maturité technologique, NDLR]. À l’issue de ce projet, nous avons atteint un niveau de TRL 6 ou 7. C’est en ligne avec nos objectifs, même si certaines étapes n’ont pas été complètement validées.
C’est donc un succès, tant du point de vue de la technologie que des produits développés. Nous avons largement dépassé nos attentes en termes de rendement, de qualité et de quantités produites, ce qui est une excellente nouvelle, compte tenu de la demande extrêmement forte de la part d’utilisateurs finaux, pour la réalisation d’essais à grande échelle.
Bien que plus de 10 tonnes de SylPro® aient été produites au cours de ce projet, la demande est tellement forte qu’en parallèle de SYLFEED nous avons également fait réaliser de grands batchs de production par des fabricants sous contrat.
Le projet SYLFEED concerne uniquement l’alimentation piscicole. Votre procédé a-t-il d’autres applications ?
A. G. : En termes de qualité, ce produit riche en amino-acides permet de remplacer complètement les sources de protéines classiques. Le bénéfice sur la santé du microbiote intestinal des animaux a également été démontré, non seulement sur les poissons, mais aussi sur des porcelets ou d’autres mammifères. Nous travaillons également avec l’INRAE afin d’étudier l’alimentation humaine et nous sommes actuellement en train d’approfondir ces thématiques d’alimentation animale et humaine, à travers un autre projet européen, le projet NextGenProteins.
Quelles sont les prochaines étapes du développement de la technologie ?
C-H. N. : Nous continuons d’améliorer nos produits et nos process de fabrications avec nos équipes de R&D aux USA. Mais nous sommes surtout engagés dans l’industrialisation de notre technologie et nous prévoyons de construire une première usine commerciale en France à l’horizon 2024.
Réagissez à cet article
Vous avez déjà un compte ? Connectez-vous et retrouvez plus tard tous vos commentaires dans votre espace personnel.
Inscrivez-vous !
Vous n'avez pas encore de compte ?
CRÉER UN COMPTE