Le Cetim vient d'acquérir une cellule robotisée capable de fabriquer des pièces en thermoplastique grâce au procédé d'enroulement de bandes imprégnées (tapes). Son objectif : optimiser cette machine pour concevoir des réservoirs à hydrogène avec ce composite tout en respectant les contraintes de coût de l'industrie.
L’hydrogène apparaît comme l’un des futurs vecteurs énergétiques pour la mobilité propre de demain. L’utilisation de ce gaz dans les véhicules nécessite la fabrication de réservoirs spécifiques pour le stocker. Pour l’instant, ils sont principalement fabriqués en composites thermodurcissables, mais de nombreux projets de recherche sont en cours pour les concevoir en thermoplastique. Ce matériau présente en effet une meilleure recyclabilité, ainsi qu’un potentiel plus élevé pour optimiser les réservoirs et pourrait aussi permettre d’accroître leur résistance mécanique. Le Cetim vient d’acquérir une nouvelle cellule robotisée conçue par l’entreprise AFPT et souhaite l’optimiser pour concevoir des réservoirs à hydrogène en thermoplastique, avec des coûts qui soient compatibles avec l’industrie.
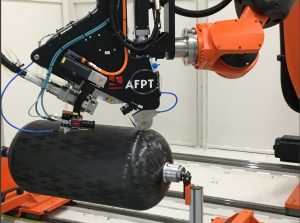
« Nous avions déjà testé un précédent modèle développé par cette entreprise allemande et l’on avait démontré l’intérêt industriel du procédé d’enroulement thermoplastique pour produire des réservoirs à hydrogène et sa faisabilité technique, notamment sur le plan de la résistance mécanique, explique Clément Callens, responsable du pôle Ingénierie des Polymères et Composites au Cetim. À présent, il faut parvenir à atteindre les exigences de l’industrie sur le plan économique en étant capable d’augmenter les cadences de fabrication. Pour y parvenir, tout se joue sur la manière d’utiliser la machine et de concevoir le réservoir en fonction du procédé utilisé. Notre travail va donc consister à optimiser ce triptyque : matière, conception et process de fabrication. »
La machine en question, appelée HySPIDE TP, fonctionne grâce à la technologie d’enroulement de tapes (bandes imprégnées), avec la particularité que la consolidation du composite se produit in situ. Pour cela, elle est équipée d’un laser qui chauffe la bande imprégnée de thermoplastique au moment où elle s’enroule sur le liner, c’est-à-dire sur la partie interne du réservoir. Ce chauffage, avec au même moment le plaquage sur le liner, permet de consolider l’ensemble en temps réel et évite toute opération supplémentaire, à la différence des thermodurcissables qui nécessitent une étape supplémentaire de polymérisation pour durcir la matière.
Une plus grande largeur des tapes pour augmenter les surfaces déposées
L’avantage principal de ce nouvel équipement réside dans le gain de temps obtenu. La tête de dépose des tapes doit permettre de multiplier par 10 la vitesse de fabrication des réservoirs, comparée à l’ancienne génération de machines déjà testée par le Cetim. Ces vitesses devraient atteindre 100 mètres de bande par minute sur le corps du réservoir et 15 mètres sur les dômes, c’est-à-dire là où sont placées les connectiques et où la structure se révèle plus complexe à concevoir. Pour augmenter les cadences de production, une deuxième piste de travail est explorée en augmentant la largeur des tapes, celle-ci pouvant passer de 10 à 40 millimètres. Certes, cette augmentation de taille aura pour effet de ralentir un peu la vitesse de fabrication, mais les surfaces déposées seront finalement augmentées.
Autre élément important : la cellule robotisée est équipée d’un magasin déporté, situé à l’extérieur, qui permet l’approvisionnement de la machine en bobines d’une longueur de 8 km, ce qui correspond aux plus grosses bobines actuellement produites sur le marché. Le fait que ce magasin soit placé à l’extérieur permet aussi d’éviter d’arrêter la machine au moment de la recharger, et donc d’augmenter les cadences de production. Les premiers résultats de ce travail de recherche sont attendus dans environ un an. « Nous allons effectuer des simulations numériques aussi bien sur le produit que sur le process de fabrication et aller jusqu’à la phase de prototypage, complète Clément Callens. En parallèle, nous allons effectuer des tests sur des cas concrets afin de garantir que cette stratégie d’enroulement de tapes puisse tenir la pression et toutes les contraintes auxquelles sont soumis les réservoirs. »
Réagissez à cet article
Vous avez déjà un compte ? Connectez-vous et retrouvez plus tard tous vos commentaires dans votre espace personnel.
Inscrivez-vous !
Vous n'avez pas encore de compte ?
CRÉER UN COMPTE