Dans l'industrie manufacturière, la robotique d'IA a évolué pour s'intégrer dans les processus de production avec des lignes d'assemblage de haute précision et des robots collaboratifs qui travaillent aux côtés des humains. C’est en particulier le cas dans l'industrie automobile qui est très automatisée. On estime que la taille du marché de l'automatisation dans l'industrie automobile pourrait augmenter de 1,95 milliard USD entre 2021 et 2026 selon une étude Technavio. L’entreprise française Inbolt s’est positionnée sur ce domaine avec sa solution GuideNOW qui permet de démocratiser la technologie de guidage par la vision en intégrant la vision 3D dans une solution conviviale, prête à l'emploi et facilement programmable par les utilisateurs finaux. Explications avec Rudy Cohen, CEO et cofondateur d'Inbolt.
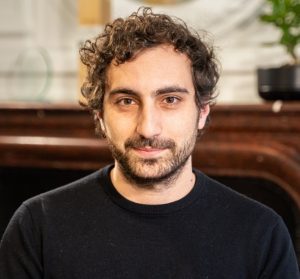
Rudy Cohen, CEO et cofondateur d’inbolt, a intégré l’École Normale Supérieure Paris-Saclay en 2015, où il s’est spécialisé en optimisation de modèles numériques, suivant un cursus Mathématiques & Computer Sciences. Après trois années consacrées à la recherche en mathématiques appliquées, concentrées sur les modèles de pollution atmosphérique et la mécanique des fluides, et fort de plusieurs publications scientifiques dans ces domaines, Rudy Cohen a poursuivi ses études dans le programme MSc X-HEC Entrepreneurs. Il a cofondé inbolt en 2019, qui développe des solutions de guidage en temps réel pour les robots industriels, basées sur la vision 3D et l’IA.
Techniques de l’Ingénieur : Pouvez-vous nous présenter votre solution GuideNOW ?
Rudy Cohen : GuideNOW est une solution de guidage robotique en temps réel, utilisant la vision 3D et alimentée par Inbrain, notre solution par IA qui permet de traiter rapidement des quantités massives de données 3D, et de déterminer la position ainsi que l’orientation d’une pièce. GuideNOW se compose d’une caméra 3D intégrée au robot d’Inbrain, notre IA de localisation de pièces d’usinage en temps réel, et de GuideNOW Studio, une application web permettant l’entraînement de nos algorithmes IA pour chaque modèle CAO ou scan 3D.
Votre solution permet de répondre à quelles problématiques industrielles ?
Notre solution répond à deux problématiques majeures des industriels. Premièrement, la flexibilité des robots : lorsqu’il s’agit d’automatiser une usine, nous avons besoin de comprendre l’environnement, car auparavant un opérateur pouvait s’adapter par rapport à la pièce à fabriquer. Le robot une fois programmé doit savoir où se trouve la pièce pour faire le même geste. Nous apportons donc plus de flexibilité aux robots en leur apportant la vision et un « cerveau » qui lui permettent de s’apercevoir que la pièce est légèrement décalée à gauche par exemple et qu’il doit donc adapter sa trajectoire.
Quelle est la seconde problématique des industriels ?
Il s’agit de la précision. Nous avons une approche software et nous avons intégré différents types de caméras, dont une qui nous permet d’avoir une précision bien meilleure. Nous avons aussi mis en place des systèmes d’initialisation qui permettent d’avoir une meilleure précision lorsqu’il y a différentes actions sur une pièce, comme la prendre ou faire du serrage. Grâce à sa mise à jour continue, GuideNOW permet au robot de voir et de comprendre la scène afin de prendre des décisions de prélèvement précises.
Comment votre solution permet-elle d’automatiser des process tout en permettant au robot d’être à la fois flexible et précis ?
Notre caméra 3D installée sur le robot sort un « nuage de points ». Nous nous appuyons sur le modèle CAO de la pièce et de toute l’infrastructure nécessaire de l’environnement (gabarits, table, cellule) pour comparer les deux données afin de vérifier que si la pièce est placée à cet endroit, la trajectoire de la machine devra être adaptée. L’ensemble du processus ne dure pas plus de 30 minutes. Cette boucle d’ajustement est réalisée en temps réel, ce qui permet d’automatiser des environnements dynamiques.
Votre technologie intéresse quels industriels en particulier ?
Tout le secteur du manufacturing s’appuie sur des robots qui font plus ou moins les mêmes process, ce sont juste les pièces qui changent. Mais notre objectif principal est le secteur automobile qui a besoin de flexibilité avec ses nombreuses lignes d’assemblage final dont l’automatisation revient très chère. Notre solution leur permet justement de réduire ces coûts. Concernant les problématiques de précision, c’est plutôt le secteur de l’électronique où forcément nous sommes sur des pièces beaucoup plus petites. Enfin, le secteur de l’instrumentation médicale s’automatise de plus en plus. Des caméras permettent d’affiner la précision sur des pièces transparentes, ce qui correspond à l’un des cas d’usage les plus développés dans ce domaine (éprouvettes, tubes…).
Vous affirmez que votre logiciel est 100 fois plus rapide (temps de réponse de 80 ms) que les algorithmes de pointe et ne dépend pas du matériel. Quels sont ses secrets ?
Ce temps de latence correspond au délai entre le moment où nous générons de la donnée 3D par la caméra et le moment où nous traitons cette information pour adapter la trajectoire du robot. Nous avons une approche d’intelligence artificielle dite hybride : nous nous basons à la fois sur du deep learning et des algorithmes plus déterministes. Au départ, nous connaissons la pièce sur laquelle nous allons intervenir grâce au modèle 3D que nous avons récupéré auparavant. Nous entraînons ensuite notre algorithme via un logiciel en amont. La machine est donc entraînée avant même d’avoir vu la pièce. Ensuite, il peut y avoir des temps de réaction et des cycles plus réduits.
Vous avez récemment signé un partenariat avec Zivid qui développe des caméras 3D de haute précision. Quel est l’objectif de cet accord ?
Les caméras que nous utilisons sont efficaces, mais les données générées ne sont pas assez « propres ». Cependant, nos algorithmes permettent d’améliorer les performances des machines. Par ailleurs, ces caméras ne permettent pas de générer des données 3D sur de petites pièces. C’est la raison pour laquelle nous utilisons les caméras de Zivid qui permettent de voir des éléments 3D plus fins d’une pièce et même de travailler sur des éléments transparents. Cela nous permet donc de travailler sur des pièces très petites, de l’ordre de 2×2 cm comme des bacs de boulons, des roulements à billes… Ce partenariat nous permet d’adresser plus de cas d’usage. Notre objectif à terme est que n’importe quel fabricant de robots puisse installer notre solution.
Réagissez à cet article
Vous avez déjà un compte ? Connectez-vous et retrouvez plus tard tous vos commentaires dans votre espace personnel.
Inscrivez-vous !
Vous n'avez pas encore de compte ?
CRÉER UN COMPTE