Créée fin 2019, la start-up industrielle Replace a développé un procédé de recyclage permettant de valoriser des matières plastiques complexes, jusqu’alors quasi exclusivement enfouies ou incinérées. Après avoir mis en service en cours d’année dernière une première ligne industrielle sur un site basé dans la Marne, Replace vient d’en lancer une seconde au même endroit et envisage de multiplier les implantations au cours des mois et années à venir. De quoi développer à grande échelle son modèle vertueux de boucles de recyclage locales.
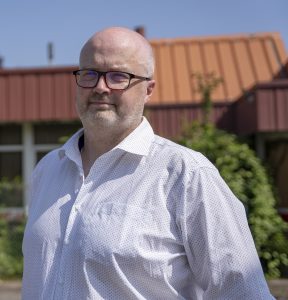
Les initiatives autour du recyclage des plastiques ne manquent pas. En dépit de son essor, la filière laisse toutefois encore sur le carreau un certain nombre « d’oubliés », tels que les décrit Laurent Villemin. Après avoir travaillé près de trente ans dans l’industrie de la transformation des plastiques et caoutchoucs, l’homme s’est ainsi lancé le défi de parvenir à valoriser ces matériaux exclus des procédés conventionnels de recyclage : plastiques multi-composants post-industriels ou post-consommation et autres emballage aluminisés jusqu’alors incinérés ou enfouis.
Aux côtés de Christian Horn, créateur en 1995 des premières palettes en plastique recyclé du marché, Laurent Villemin a fondé Replace en novembre 2019. « Nous avons cherché à inventer un concept qui permettrait de traiter ces flux “oubliés” ; et ce non pas en les retriant, mais au contraire en les mélangeant », retrace Laurent Villemin, aujourd’hui président de Replace. « L’idée était de profiter des additifs déjà présents dans les différents plastiques, afin de ne pas avoir à en ajouter, et d’avoir malgré cela un process performant », ajoute le co-fondateur de l’entreprise basée en Moselle, dans la région Grand Est.
Les deux spécialistes ont ainsi développé un procédé inédit – et breveté – permettant une transformation directe des plastiques en mélange, en un produit fini lui-même recyclable. Le tout en une seule et unique étape. « Techniquement, il s’agit d’une forme d’injection, avec plusieurs modifications permettant d’avoir des performances accrues », décrit Laurent Villemin. De ce procédé breveté est ainsi née une véritable solution industrielle conçue en partenariat avec AISA, leader mondial des machines de production de tubes plastiques et laminés.
Une première ligne mise en service en 2021
Bénéficiant notamment d’un dispositif d’incubation mis en place par la Région Grand Est et d’aides de l’ADEME, la start-up industrielle est ainsi parvenue à lancer en cours d’année dernière sa première ligne de production. « Le projet a abouti en un temps extrêmement court. Nous avons été portés par notre élan ! », s’enthousiasme Laurent Villemin. Depuis le 2 janvier dernier, c’est même en « 3×8 » que tourne le site industriel basé dans la Marne. Une usine que Replace a voulu implanter au plus près du gisement de déchets à valoriser. « Ce démonstrateur capte des déchets qui sont produits dans un rayon de moins de cent kilomètres », souligne Laurent Villemin. Un gisement constitué notamment par des coiffes de champagne, qui, après transformation via le procédé Replace, donnent naissance à des tuteurs utilisés dans les vignobles de la région. « C’est vraiment cette logique locale qui nous motive. Nous avons conceptualisé cela avec ce que nous appelons le “Local³” [local au cube, n.d.r.] », dévoile le président de Replace. Un concept labellisé depuis avril 2021 par la Fondation Solar Impulse et basé sur le triptyque « locally sourced, locally transformed, locally used[1] ».
Outre ces tuteurs baptisés Tutofi, déjà écoulés à plus d’un million d’unités en partenariat avec l’entreprise KeepFil et fabriqués à partir de plus de 500 tonnes de déchets plastiques, Replace se penche également sur la production de palettes, ou encore de solutions d’agencements pour les commerces. « L’objectif est de montrer que les produits que nous pouvons réaliser ont une qualité suffisante pour répondre aux besoins de marchés exigeants, pour des usages premiums », justifie Laurent Villemin, avant de préciser que le procédé développé par Replace se destine avant tout aux produits longs et épais. « Nous n’allons pas concurrencer l’injection sur des articles tels que les coques de téléphone ou des bouchons, chacun son métier », glisse le président de Replace, qui prône ainsi la complémentarité des solutions de recyclage, plutôt que la concurrence frontale. « Il faut un arsenal de solutions pour ouvrir le champ des possibles », considère Laurent Villemin.
Côté empreinte carbone, l’analyse de cycle de vie réalisée par Replace montre un net avantage des tuteurs en plastique recyclé produits par l’entreprise par rapport à leur équivalent en plastique vierge, et même en bois. « Le fait de les produire localement permet en effet de drastiquement limiter les transports », souligne Laurent Villemin.
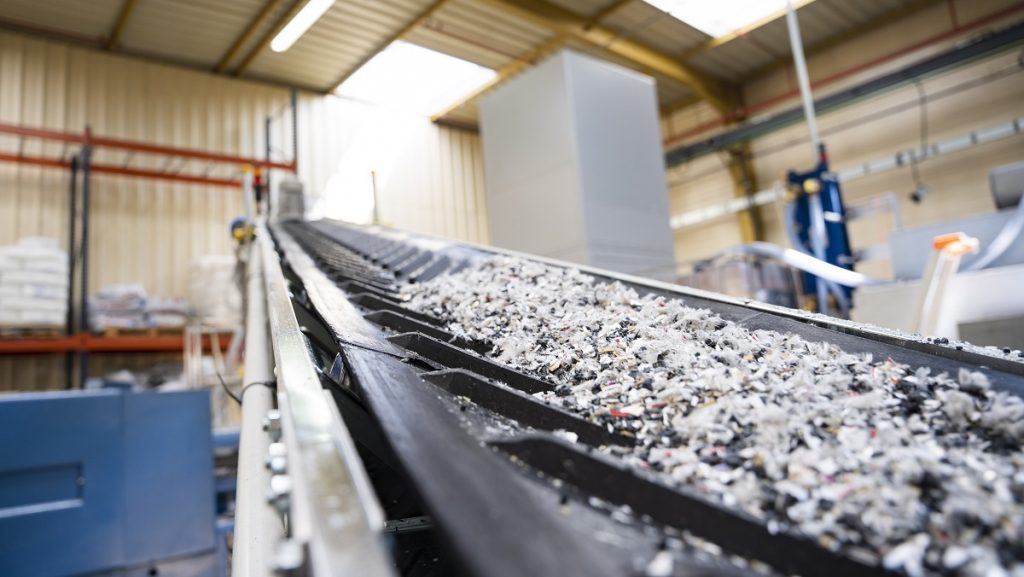
Vers un déploiement à grande échelle
Après avoir démontré l’efficacité de son procédé dans son démonstrateur marnais, Replace a lancé il y a peu une seconde ligne de production dans cette même usine, avec l’ambition d’en augmenter les capacités, mais également d’élargir la gamme de produits fabriqués à partir de déchets plastiques jusqu’alors impossibles à recycler. « Il s’agit d’une ligne de deuxième génération, qui bénéficie des centaines de points d’amélioration identifiés sur notre première ligne », précise le président de Replace.
Et pour 2023, c’est même un deuxième site bien distinct de l’usine marnaise que la start-up envisage de construire. Le début d’un déploiement à grande échelle a été permis notamment par une levée de fonds d’un montant de 4 millions d’euros, annoncée en septembre dernier. L’entreprise, qui compte actuellement une dizaine de postes en équivalent temps plein, espère par ailleurs atteindre le seuil d’une quinzaine de salariés d’ici à la fin de l’année. « Nous sommes dans une logique de montée en puissance progressive, de crescendo », note Laurent Villemin. « Notre objectif est véritablement de mailler le territoire avec des sites comportant entre deux et six lignes tout au plus », complète le dirigeant. Des lignes qui peuvent, en outre, être gérées par des employés sans expérience préalable en plasturgie. « Avec Christian Horn, nous avons voulu aller vers une logique gagnant-gagnant pour tout le monde, avec un accent particulier mis sur l’emploi. Nous avons eu à cœur de développer un modèle de ligne pouvant être opérée par des salariés issus par exemple d’entreprises adaptées, comme cela a été le cas lors de notre démarrage. Nous avons prouvé que cela fonctionne », conclut Laurent Villemin, qui voit finalement en Replace une sorte « d’alambic du plastique » : une solution permettant de valoriser au plus près les fruits d’une production locale.
[1] Approvisionné localement, transformé localement, utilisé localement.
Réagissez à cet article
Vous avez déjà un compte ? Connectez-vous et retrouvez plus tard tous vos commentaires dans votre espace personnel.
Inscrivez-vous !
Vous n'avez pas encore de compte ?
CRÉER UN COMPTE